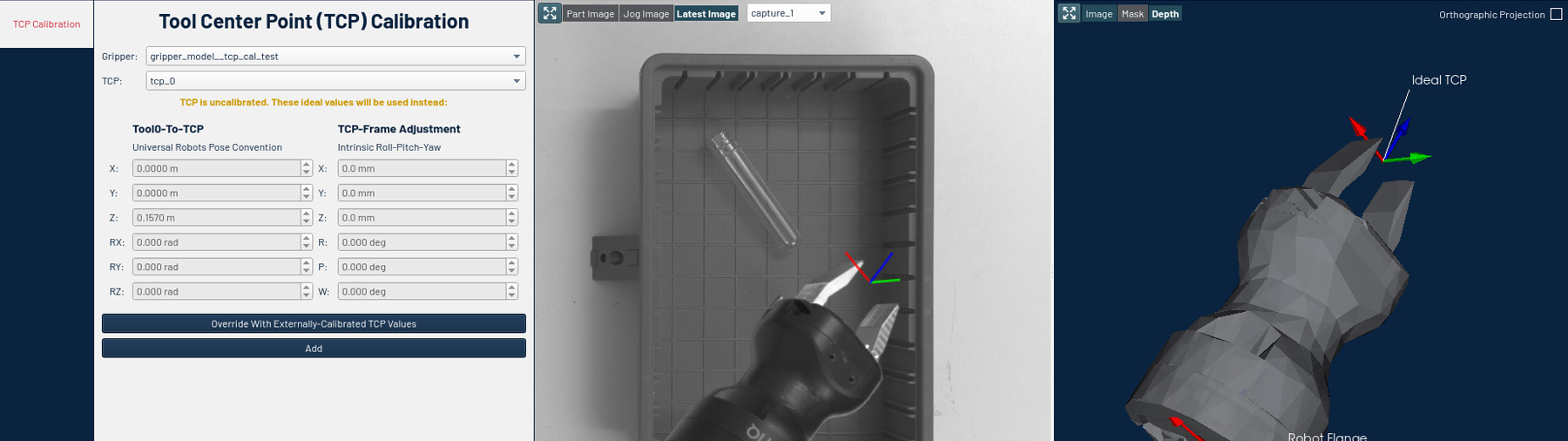
Apera Vue 9.50 is here—with 4D Vision built for your real-world plant floor
At Apera AI, we know the plant floor doesn’t always play by the rules. Bins shift. Grippers wear. Vision calibration drifts. Lighting conditions change. While traditional 3D vision systems struggle with these everyday realities, Apera Vue 9.50 is designed to thrive in them.
“With Vue 9.50, we’re helping customers adapt faster to the unexpected, because no two racks are the same after six months on a factory floor. We’re solving problems with true AI that no other vision system can solve. Only Apera Vue can unlock the highest levels of manufacturing performance, speed, and precision at scale with 4D Vision.”
—Sina Afrooze, CEO and Founder, Apera AI
This release brings our most advanced 4D Vision software one step closer to human-like vision and intelligence—giving robots the ability to see, understand, and adapt to variation in real-time. With tools for smarter calibration, performance diagnostics, and deployment optimization, Vue 9.50 helps unlock the power of 4D Vision-guided robotic automation, with less time spent tuning, guessing, or restarting.
If your production lines are still human-dependent for bin picking, de-racking, and other assembly operations, read on to explore what’s new with Apera Vue!
Adapt to Real-World Variation with AI
Real-world conditions rarely meet the expectations of idealized vision setups. Vue 9.50 introduces two major features that boost accuracy and reliability, even when the environment around your robot changes.
Vision-Based Bin Finding
When bins are swapped, bumped, or slightly misaligned between cycles, traditional bin-picking pipelines struggle. Now, Vue 9.50 can automatically detect and adjust for bin shifts (in X, Y, and yaw) using 3D vision data and AI (the 4th dimension)—without requiring manual re-teaching or reconfiguration.
Once the bin’s nominal size and location are set, Apera Vue continuously refines its position using actual 3D input. This is especially useful when bins are not precisely fixtured, or when changeovers introduce subtle yet critical variation.
Take advantage of these new capabilities!
- Triggerable pipelines can be initiated via the Vue UI or by the robot using the same API interface as standard picking lines, no changes needed.
- Independent and reusable, Vue runs separately from the pick pipeline, storing updated bin position for future use.
- Safe by design, Vue clears previously stored data to avoid unexpected behavior if a bin correction fails.
- Lightweight impact is achieved by avoiding cycle-time overhead. Vision-based bin finding runs only when bin changes are detected, not for every run pick.
- Portable and persistent, correction data is saved with session recordings and carried across restarts for better support and repeatability.
This feature improves bin picking reliability and adaptability—reducing downtime in unpredictable environments and bringing vision-guided robotics closer to plug-and-play performance.
Vision-Guided TCP Calibration
Small changes in EOAT geometry can have big effects on picking accuracy. A worn or misaligned gripper can shift the robot’s true tool center point (TCP), creating errors in motion planning.
Vue 9.50 introduces Vision-Guided TCP Calibration—a powerful new tool that lets you calculate sub-millimeter accurate TCP poses directly from vision data. Say goodbye to traditionally slow and imprecise methods like manual trial-and-error or the 4-point approach.
Vue’s new approach leverages its vision system to compute TCPs more precisely and robustly—simply grasp or position the part in different locations and orientations throughout the cell, capture each setup with vision, and fit a corrected TCP pose based on the collected samples.
How it works!
- Vision-based TCP alignment enables Vue to calculate true tool0-to-TCP transform using 3D vision, robot pose, and part localization—no probing or alignment routines required.
- Multi-sample fitting supports calibration using multiple angles and locations captures to generate a best-fit TCP transform.
- Orientation-agnostic, Vue accounts for depth and pose estimation errors by averaging across diverse post and grasp configurations.
- Support for complex grippers allows Vue 9.50 to calibrate each TCP independently for multi-head or asymmetric grippers, even with variations in physical geometry.
- Structured UI workflows reduce mistakes and ensure high-quality calibration results with new “TCP Classroom” guides that walk you through each step.
Now you can save time by performing high-accuracy, vision-aligned TCP calibration directly within Vue 9.50. The result is faster, more accurate picks, predictable robot motion, and enhanced repeatability.
Optimize System Performance
When it comes to system performance, visibility is everything. Vue 9.50 gives you new tools to speed diagnostics and fine tune performance—putting you in control.
Recording & Playback System
A new and comprehensive Recording & Playback System allows you to capture, view, and export image and vision data right in Vue 9.50. It’s now significantly easier to diagnose issues, fine-tune performance, and collaborate with technical support.
How you benefit!
- Automated recording triggers can be configured to record automatically when anomalies occur, like excessive cycle time, vision failures, or pickability issues.
- In-app playback lets you see exactly what triggered the event and replay the scenario for quick insights.
- Pipeline optimization is made possible by using recordings to evaluate, fine-tune, and optimize settings.
- Export recordings easily and share them with the experts at Apera Support for enhanced collaboration and faster resolution.
The new Recording & Playback System gives you greater visibility and control—to speed up resolution and enable more proactive system optimization.
Accuracy Insight
This new guided analysis tool is designed for proactive performance tuning and troubleshooting robotic cell issues that impact precision. Accuracy Insight provides a structured approach to validating calibration, evaluating system alignment, and understanding how different components contribute to accuracy—enabling more reliable picking, smoother changeovers, and sustained long-term performance.
Explore these new capabilities!
- Calibration analysis allows you to verify stereo calibration, hand-eye alignment, and robot model accuracy through a guided, multi-step process.
- Reference checkpoints allow you to compare tool and pattern motion across multiple robot poses to identify where inaccuracies arise.
- Visual diagnostics give you clear, visual breakdowns of translation and rotation errors—with insight into whether the source is robot or vision-related.
- Guided correction steps are provided when misalignment is detected—Vue 9.50 provides actionable next steps, such as redoing hand-eye calibration with more variance in the robot movement.
- Integrated workflows means all checks and updates are now built into the Vue interface— making it easy to perform regular accuracy reviews without extra tools or documentation.
It’s now faster and easier to optimize performance and protect uptime. With Accuracy Insight, your team can analyze system accuracy, pinpoint root causes of error, and make informed improvements—enabling more reliable picking, smoother changeovers, and sustained long-term performance.
Accelerate Setup and Calibration
Are you looking to power up new robotic cells with Apera’s 4D Vision? Vue 9.50 helps you go from setup to plant operation faster.
Placement Groups
When setting up pick-and-place applications, it’s common to have multiple placement points per part. Vue 9.50 now simplifies setup. Save time and reduce complexity by grouping placement points—this allows a range of points to inherit or transform the placement path from a central point, enabling simple placement.
Upgraded Calibration Boards for Hand-Eye Calibration
Apera 4D Vision systems now ship with upgraded calibration hardware—the new rigid aluminum-composite ChArUco calibration boards with mounting brackets are designed to dramatically improved calibration quality.
These boards combine checkerboard and ArUco marker detection, significantly improving the accuracy, repeatability, and robustness of the hand-eye calibration process.
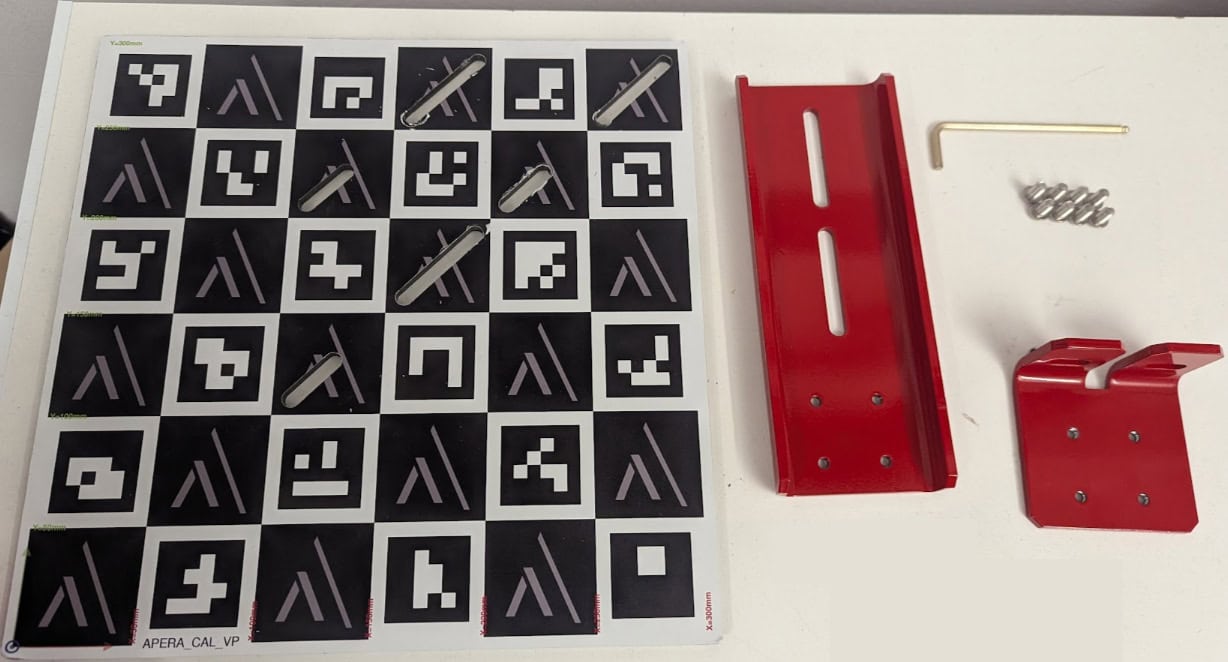
Key capabilities:
- Improved calibration accuracy is achieved with substantially better pose estimation (than single-marker techniques), especially in EOAT-mounted (eye-in-hand) scenarios.
- Industrial-grade rigid backplates ensure the boards maintain consistent geometry and durability in manufacturing environments.
- A mounting bracket included with each kits offers flexibility—mount your VuePort cameras on directly to the robot’s J6 flange or end-of-arm tooling (EOAT).
- Standardized across Apera systems, every new 4D Vision system includes a ChArUco calibration board kit to streamline deployments and optimize field calibration.
- Optimized for Vue workflows, the kits is fully supported in Vue’s hand-eye calibration and Accuracy Insight workflows, enabling consistent part-to-robot alignment.
Achieve more accurate hand-eye calibrations, faster—with fewer retries, more robust results, and better alignment between robot motion and vision data. This new hardware lays the foundation for reliable automation performance on day one!
Get more from your 4D Vision system—starting today!
Vue 9.50 is more than an upgrade to your 3D vision system—its innovative new features promise to unlock performance on your real-world plant floor.
🔴 Already using Apera Vue?
Contact your expert Apera Support team to upgrade to Vue 9.5.
And, explore the release notes to dive into each new feature!
🔴 Curious about 4D Vision?
Get started with Apera Vue today!