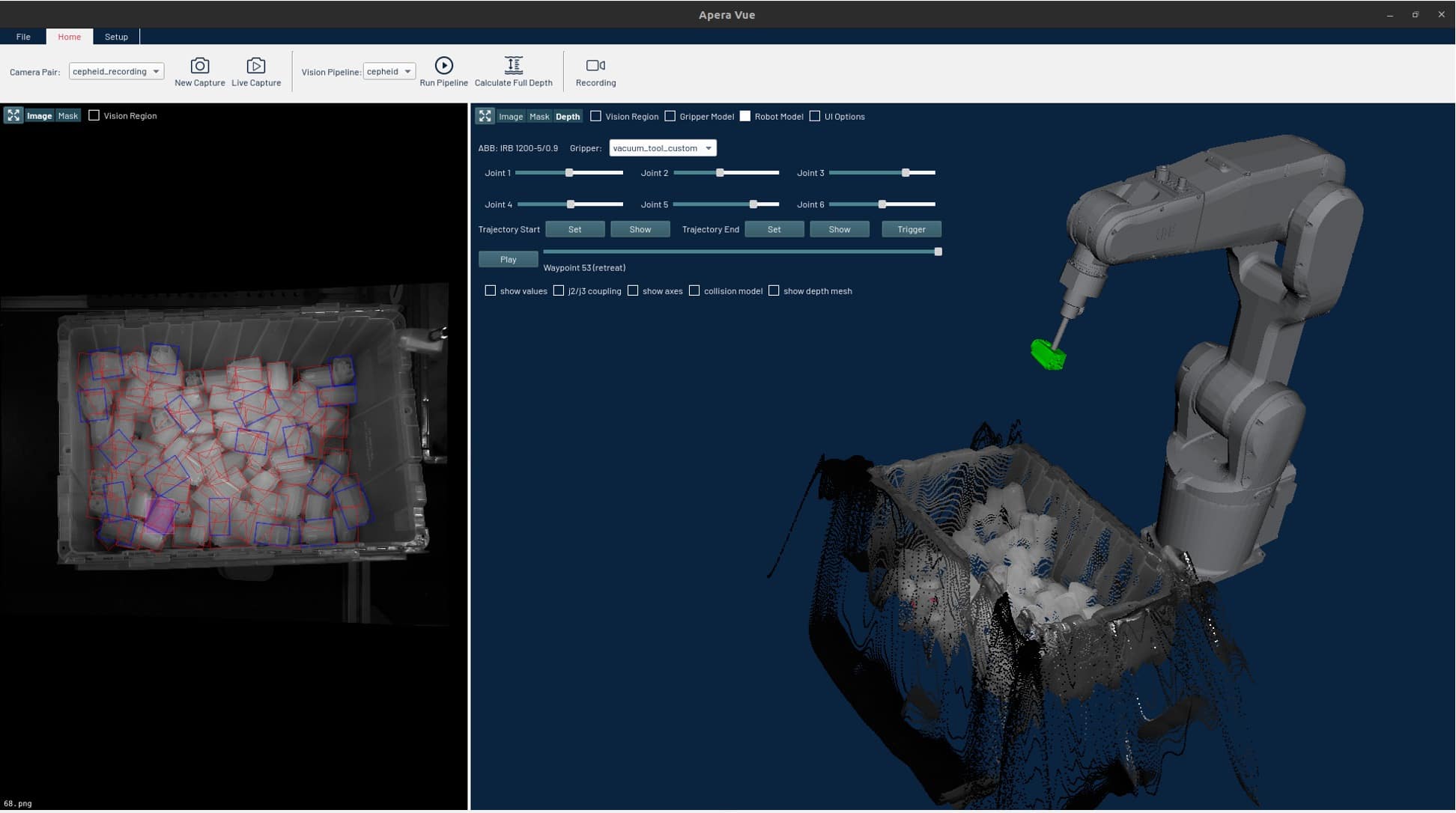
What’s new in Vue?
Innovations in AI make vision-guided robotics easier to use and reduce automation risk
What’s new in Vue?
The success of a robotic cell depends a lot on Vue’s ability to identify objects. Those powers in Vue are as good as ever. What’s new is a host of features that allow automation professionals to control and optimize the implementation of the AI-powered vision program.
Enhanced control over vision implementation
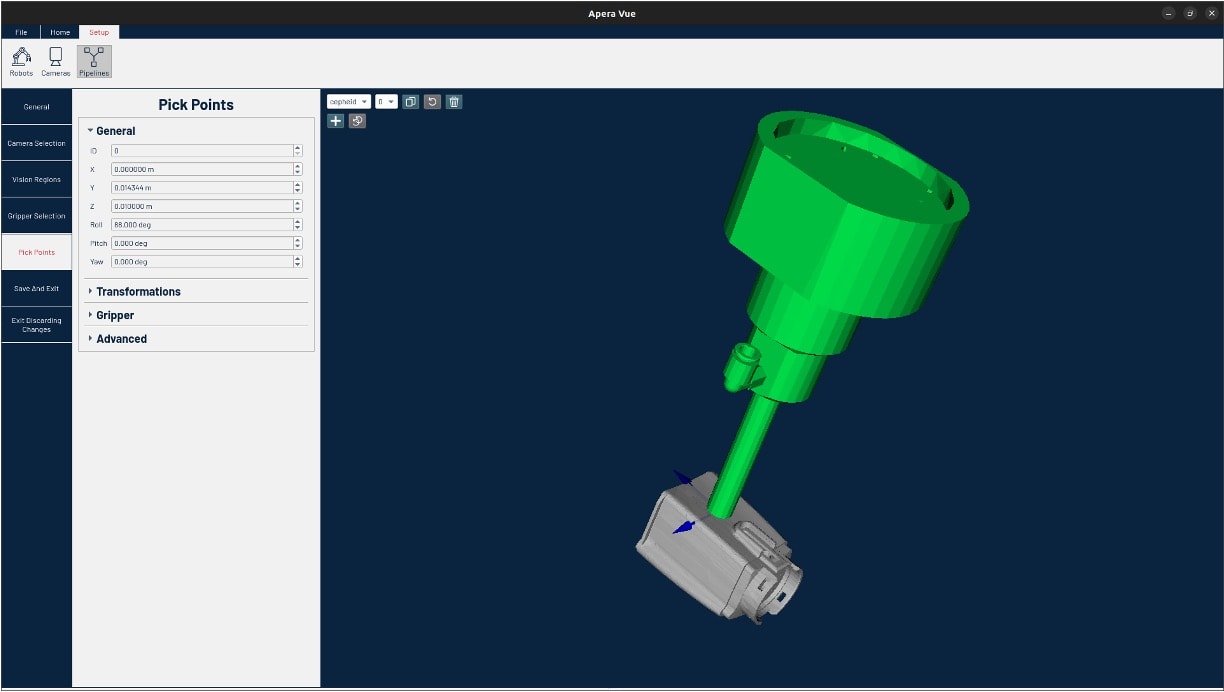
Vue has always taken care of the vision programming tasks, but now also adds more control over the implementation of vision. Vue now builds in more control over choosing pick points, approach angles in and out of robot moves, and avoiding interference with adjacent objects in Dexterity, Apera’s two-finger gripping intelligence.
Using these innovations, engineering teams can implement or improve vision-guided robotics more easily and without specific vision expertise. The engineer working in Vue can improve the productivity and reliability of the robots in a cell using built-in software tools.
Reducing the risk of complex robotic automation
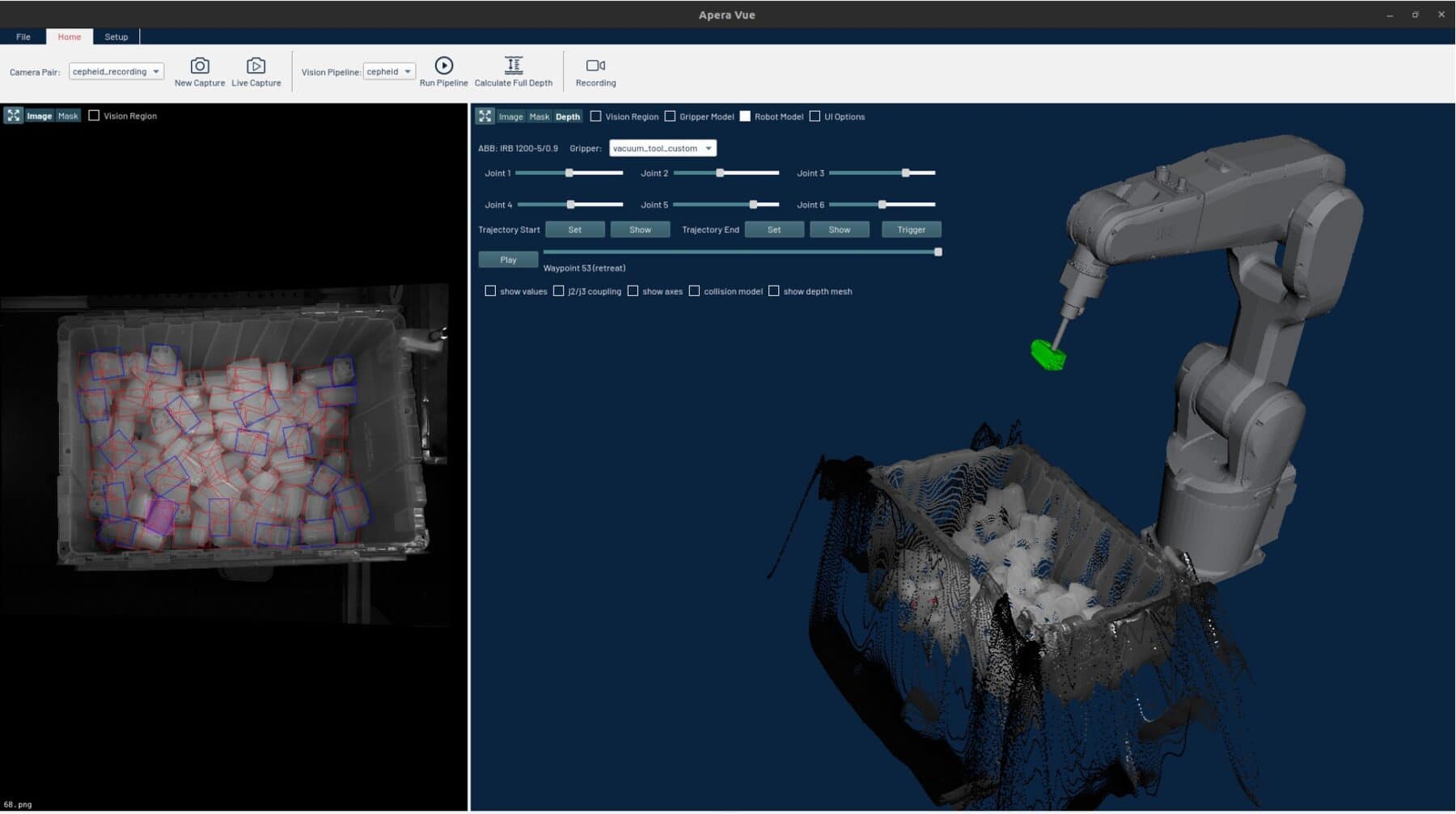
Autopilot is Apera Vue software’s feature that enables safe paths in and out of moves. Autopilot identifies the object, guides the robot’s movement and helps it avoid singularities or collisions.
But before an engineer tells the robot to move, Autopilot can now simulate the automation within the real, fully built cell. Ahead of an automation investment, this means knowing the robot, gripper and cell design will perform the way you expect. Once installed, it gives you extra assurance that you’re all set to perform the task quickly and reliably, even when new tasks enter the picture.
Gripping strategy takes a leap forward
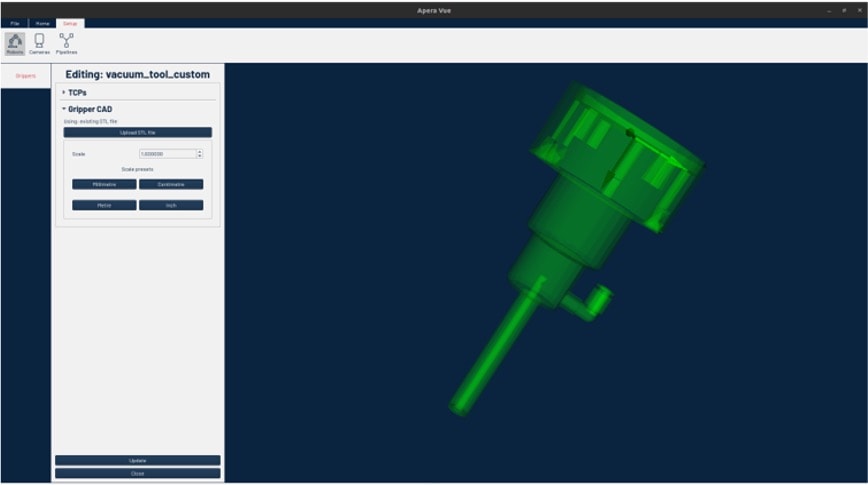
Vue now builds in more control over choosing pick points, approach angles in and out of robot moves, and avoiding interference with adjacent objects in Dexterity, Apera’s two-finger gripping intelligence.
We have seen in our customers’ sites that custom end-of-arm tooling can be a challenge to the performance of a vision-guided cell. In Vue, you can upload a CAD model of the end-of-arm tool (EOAT) and achieve excellent EOAT to object orientation. That matters a lot in assembly or material handling applications where a part must be precisely placed for the next step of manufacturing. Our Tier 1 automotive customers tell us this ability is amazing, enabling them to have two robots work together more reliably and lowering the risk of custom EOATs.
Considering vision for your next robotics project?
Get in touch with the experts at Apera AI to discuss your automation needs.