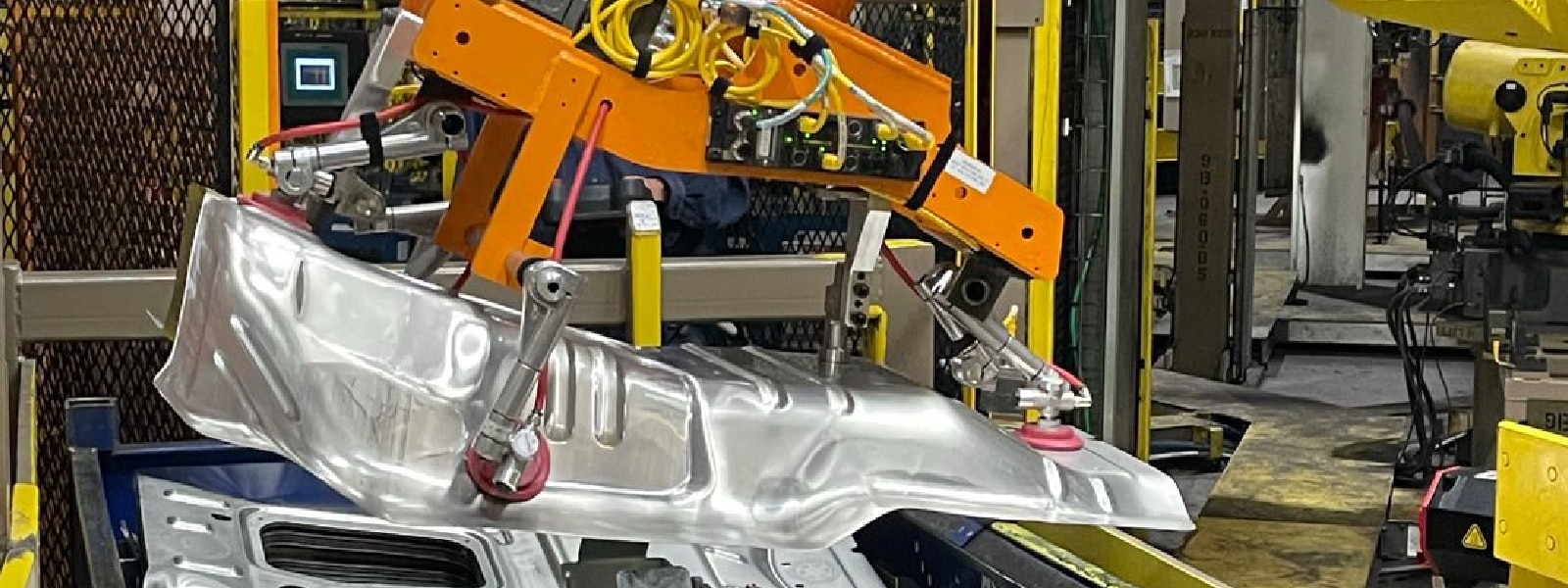
Ford Super Duty Plant makes improvements to quality, efficiency and cost by adding vision-guided robot
Summary
A manufacturing step was being performed by an operator at Ford’s Super Duty Body Shop within Kentucky Truck Plant was struggling with the handling of large stamped metal automotive parts from a dunnage on to a stack. A cell was created to automate the process using a FANUC industrial robot. Assistant Plant Manager Todd Ashton credited the UAW Skilled Trades, Apera AI and its partner Air Hydro Power for “improved quality, efficiency and cost” following the retrofit of the cell using Apera AI’s 4D Vision technology.
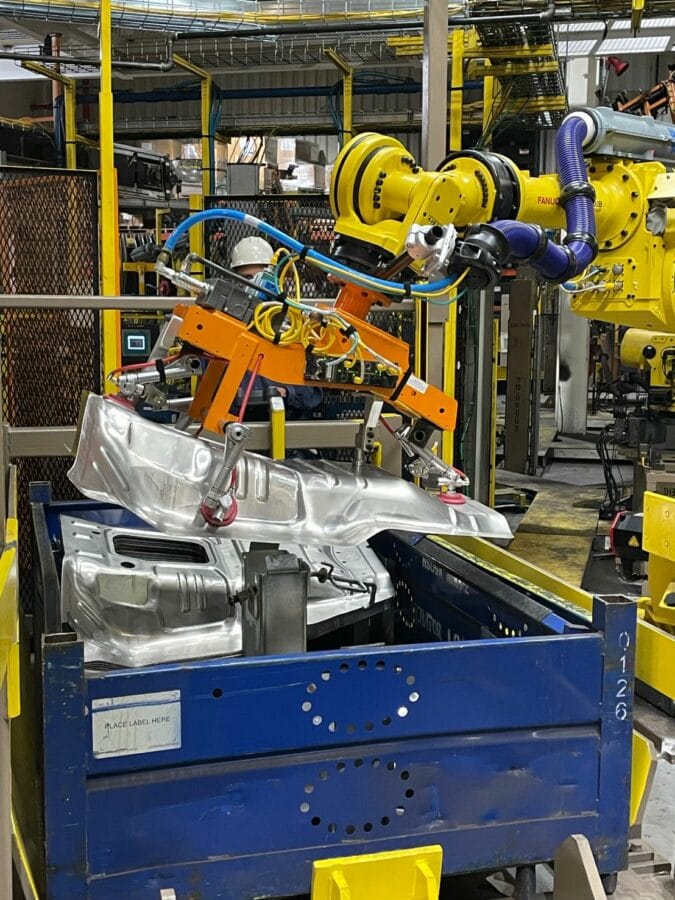
Project scope
This new cell retrofits a previously manual process where an operator would perform this step in the manufacturing process. These stamped metal parts are used in Ford’s truck assemblies.
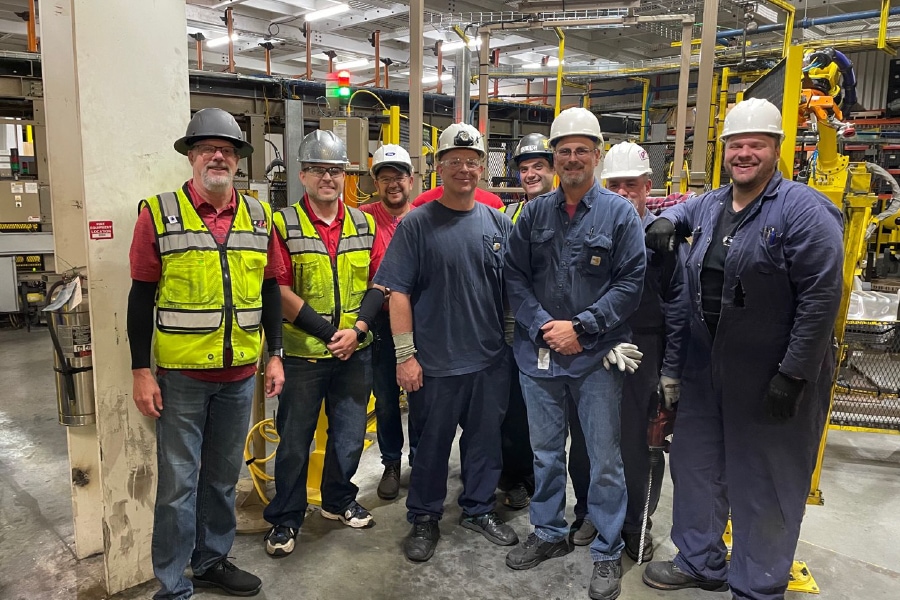
Project results
The robotic cell design replaced the manual process and has been operating to Ford’s satisfaction since the installation. Here is some feedback from the project team:
From the project’s toolmaker: “We started searching for a vision system that was out of the box so we could integrate ourselves with minimal vendor support. The apparel system seemed to be all of that. We had this system locating parts in our lab setting in less than two days. Everything about the Apera AI vision solution was well within our ability to handle in a very short period of time. This is the main thing that I see as a huge advantage over the other systems that we use today.”
From the project’s electrical engineer: “From my perspective, the main qualities that have separated Apera from previously tried vision systems would be: 1. Accuracy. With some reasonably easy calibration of the cameras and then the robot to the cameras, we have achieved robot-to-part accuracy that we have not seen with other solutions. 2. Simplicity. With a bit more work on the front end to provide Apera AI with an accurate model of the part you are picking and robot end effector, the installation and setup was relatively simple. I have no reservations about using Apera vision for robot guidance in future projects.”
From the project’s controls engineer: “I was first exposed to vision-guided robotics 26 years ago. In this time frame, I have yet to see a vision guided robotic system set up faster, simpler or more effectively than what the team just accomplished with Apera AI.”
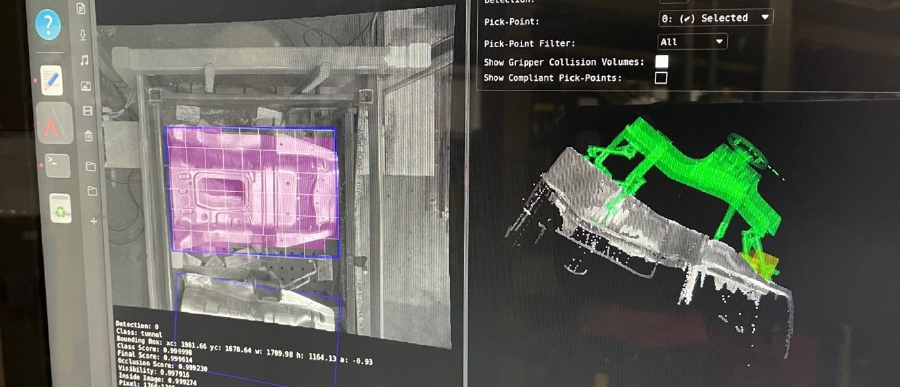