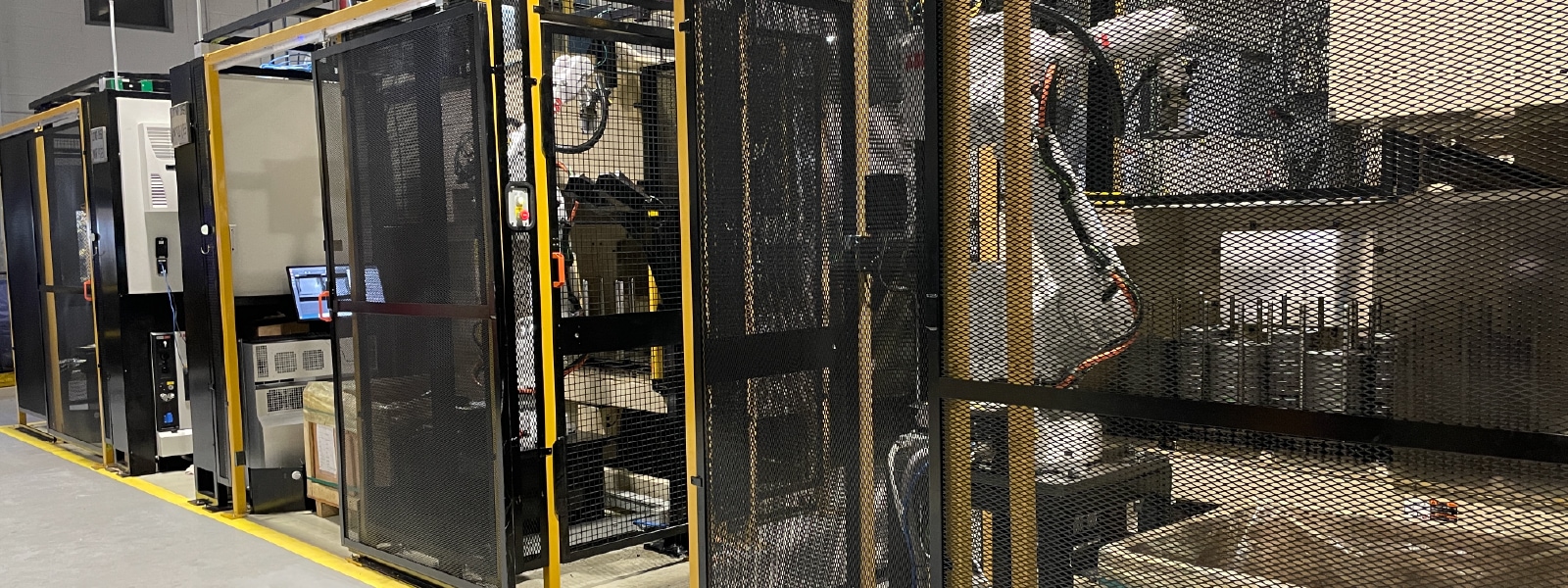
Linamar automates random bin picking with Apera AI x ABB Robotics
Summary
Hastech Manufacturing, a division of Linamar Corporation, was manually loading unmachined automotive parts for processing. Linamar is a Tier 1 automotive supplier headquartered in Guelph, Ontario, Canada. While dealing with labor shortages and wanting higher productivity, they turned to ABB Robotics and Apera AI across three robotic cells. They automated the process—improving efficiency and focusing their operators on quality and productivity.
Project Scope
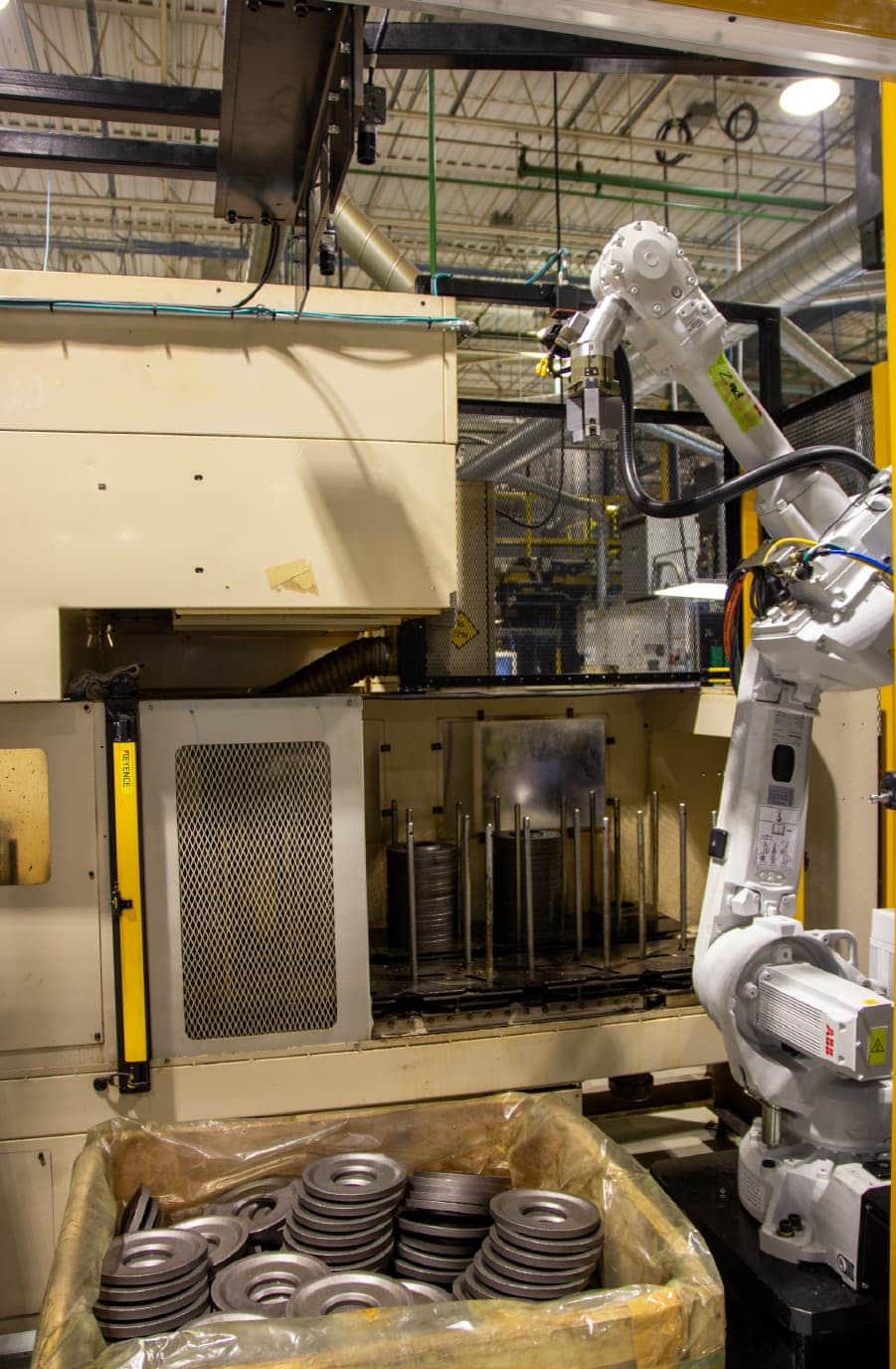
Across three machines, Linamar operators were responsible for loading unmachined transmission discs on to the machines’ feeder system. Due to labor shortages, Linamar wanted to automate this process. They chose a combination of ABB Robotics industrial robots and Apera AI’s Vue robotic vision software. After success with the initial cell, the same solution was implemented across the remaining two cells.
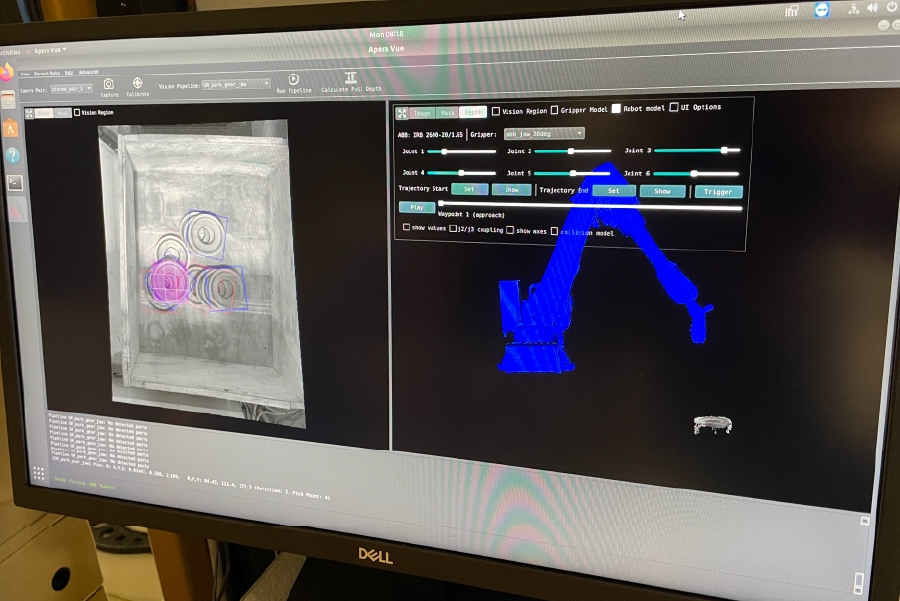
Project Results
All three cells are now successfully picking, allowing Hastech’s operators to focus on quality of the automotive parts leaving the machine and the machines’ productivity. ABB’s robots seamlessly perform the job using a custom end-of-arm tool that picks through the center of the disc. Linamar is working with both providers to implement the technology elsewhere in its operating companies.
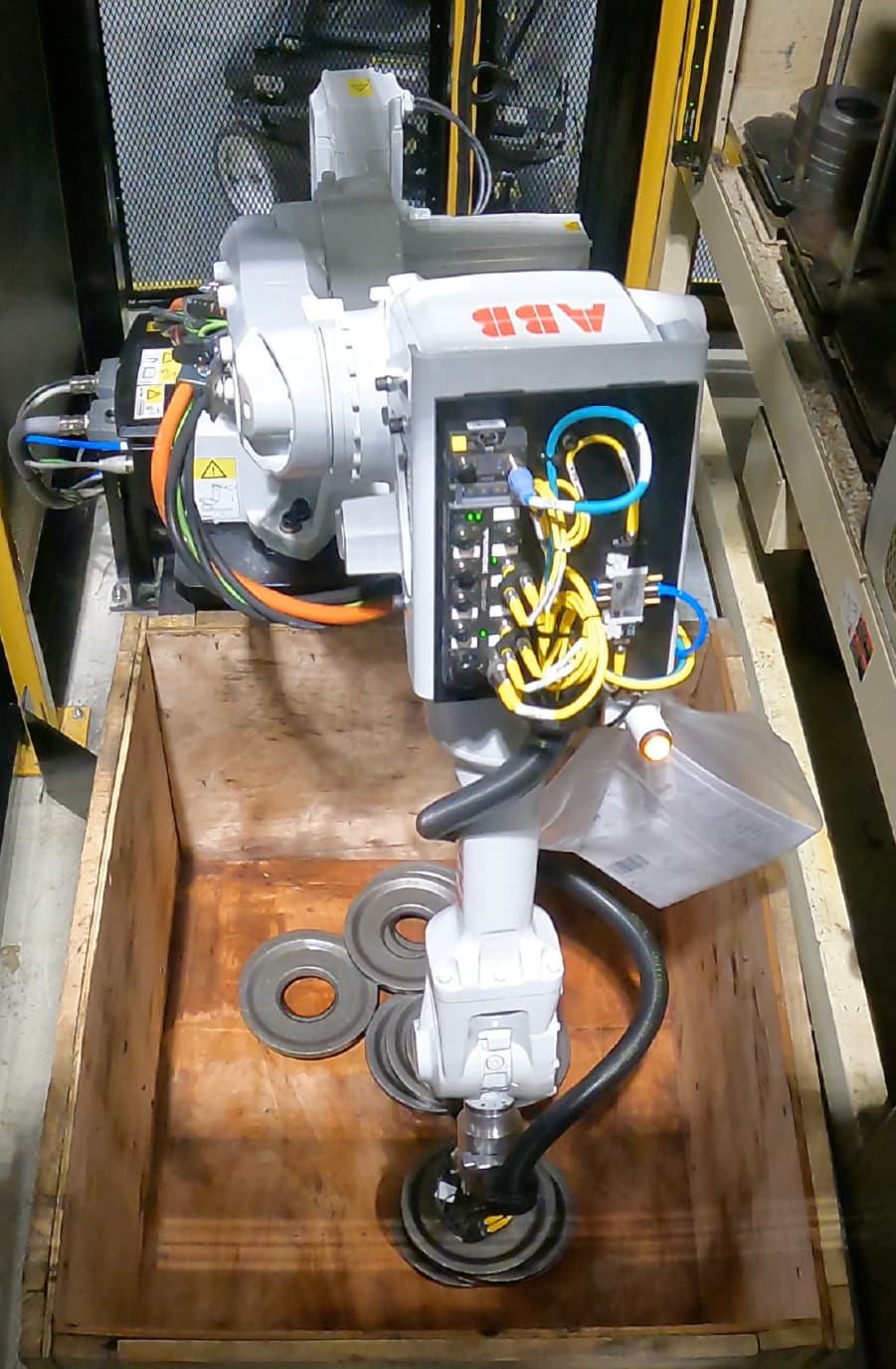
Random bin picking of the unmachined discs is challenging for a few reasons. The bin is deep and lined with plastic that interferes with visibility. Lighting is a big problem in vision, but Apera AI’s technology can work even in the irregular lighting and shadows within Hastech’s facilities. And the parts are covered in grease that interferes with visibility as well. When emptying the bin, the Apera vision system must guide the robot into the corners and avoid collisions with the sides as it moves the part out of the bin.